Were he wearing green coveralls and work gloves, you might recognize Davis from his work with The Plant Operations recycling team. But during school hours Davis is putting advanced drafting software to use designing a heat recuperator for Fire & Light's three production furnaces.
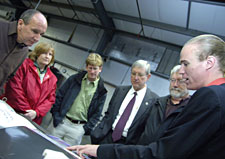
The heat recuperator works by capturing some of the wasted heat energy from the furnace's exhaust gases and using the captured energy to pre-heat the furnace combustion air. The 2500-degrees-Fahrenheit exhaust passes through a series of heat exchange surfaces in the recuperator where it elevates the incoming combustion air temperature to around 650 degrees. The pre-heated combustion air is then mixed with natural gas in the furnace’s burners resulting in a 30% reduction in natural gas usage. "The (heat recuperator's) fluted design will vortex air in stainless-steel tubing. Increased surface area pulls more heat off before it goes back to the furnace," said Davis.
"What we're doing is we're pushing air exhaust through a controlled environment, pulling off as much heat as possible," said Dr. Russell who worked with Davis on the project. Pre-heating the combustion air allows the furnaces to burn more efficiently, resulting in the energy savings, Dr. Russell explained.
The designs for the recuperator were presented to a group that included HSU President Rollin Richmond, Maggie Gainer, director of the Office of Economic and Community Development (OECD), Dr. Richard Paselk from the Department of Chemistry and Fire & Light owner John McClurg. The OECD was involved in this project from the onset, pairing Ben Davis's work with Fire & Light using federal money. "The OECD had a U.S. Economic Development grant that assists companies with potential for growth, like Fire & Light. And Ben Davis' project, through applied technology working with the faculty there, was a good match," said Gainer.
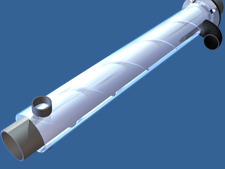
Davis, who has been working with Fire & Light as an intern is ready to go to work for them as his graduation inches closer. As of publication, Ben only has to make it through finals week before he's awarded his Bachelor's of Science in Industrial Technology. After that, Davis hopes to get to work installing the recuperator. "We were ready to go with this thing a month and a half ago but I said 'we can't do it right in the middle of Christmas season,'" said McClurg.
The company, which turns out somewhere between 600 and 700 pieces a day, expects to miss two weeks of production while the recuperator is installed. Once installed, the energy savings will go toward, in part, doubling Fire & Light's production capacity as the company prepares to install three more furnaces and expand its product line in the near future.